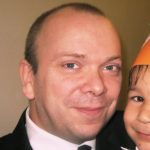
Peter Marsh
@
When it comes to the installation of your pallet racking system it is vital that the installation team is experienced and professional and have all the necessary qualifications and accreditations to ensure the job is done properly. A pallet racking system that collapses can be a huge threat to your business – costing hundreds of thousands of pounds of damage to stock, potentially causing serious harm to staff or visitors near the system at the time of the collapse and potentially bringing your business to a close, at least temporarily.
Fortunately, it is an uncommon occurrence, but it is something you need to be aware of. The collapse of a pallet racking system is entirely preventable and will only happen due to poor quality materials, poor quality installation or improper training and unmaintained racking.
What Can Cause a Pallet Racking System to Collapse?
Overloading Your Pallets
Never overload your pallets, not only will this damage the pallet causing the timber to fracture and collapse (especially the runners). It will also contribute to overloading the beams and frames of the pallet racking system.
- Stick to and know the manufacturers recommended weight limits for loading weight on your system.
- Always buy new pallet racking over second hand as a quick respray can cover many a hidden danger such as oxidation and rust. Without any provenance you will never know if the structure has been consistently overloaded, no matter what the seller says.
- Display load notices at all times so staff and forklift divers are aware of the weight limits.
- Different type of stock requires different types of pallet racking, make sure you are using the right pallet racking system for your stock.
Collapse Due to Forklift Collisions
This is by far the most common cause of pallet racking collapse, sometimes just a simple clip of an upright can cause the whole system to collapse.
- Make sure all drivers have received proper training before operating a forklift.
- To reduce damages and collapse, a racking protection system should be installed, for example, column guards and end of racking barriers.
- Make sure your warehouse pick system has adequate aisle space between racks.
- Implement speed restrictions for any vehicle operating in your warehouse.
- Floor marking systems can reduce warehouse accidents and damage to racking systems.
- Make sure the operative is using the right forklift for the right job and make sure aisles are kept clear.
Incorrect Installation and Use of Bad Pallets
A pallet racking system that is incorrectly installed or is installed using bad pallets is more likely to collapse or become damaged.
- Make sure you use a reputable, accredited and professional company to install your racking systems.
- Look for SEIRS registered installers who will make sure the installation of the racking system is in line with SEMA guidelines.
- Purchase your racking system from a reputable UK or European manufacturer.
- Avoid trying to integrate different manufacturers into the same systems.
- Check for broken or unsecured pallets.
Negligence When It Comes to Pallet Racking Maintenance
Pallet racking maintenance should never be overlooked. Maintenance and inspections meet SEMA and FEM guidelines, and all the latest UK HSE regulations.
- Routine inspections should be carried out by a reputable independent organisation (i.e. one that is not carrying out the subsequent repairs) who is impartial, you can find more information on our inspection service here.
- Make sure there is a process in place to report any damaged warehouse racking.
- Do not use any racking that is broken or faulty until it is repaired. We recommend taping off the affected bays as a precaution.
- Always use pallet racking systems in line with manufacturers guidelines.
Untrained Staff
Staff negligence can also cause pallet racking systems to collapse, even with the most effective safety measurements in place.
- Make sure all staff attend safety training and are aware of rack safety.
- All staff should be made aware of the dangers of poorly maintained racking systems.
- Implement a process to report any damaged pallet racking, either caused by the individual or someone else.
- Reduce incidents by increasing supervision or management of staff.
- Do not allow staff to climb on racking during the picking process.
By neglecting any of the above points you are potentially putting your staff, visitors and business at risk and potentially opening yourself up to huge fines, prohibitions notices and prosecution. Please bear in mind the following when you neglect to look after your pallet racking system:
- PUWER Fines – Failure to keep working equipment (including pallet racking) in safe and working order can result in large fines and even prosecution from HSE.
- Damage and Loss of Stock – A pallet racking collapse will almost certainly result in devastation or damage to stock. This will be a direct cost to the business to replace.
- Business Closure of Downtime – The HSE could potentially launch an investigation resulting in closure or downtime of your business until an understanding of how the collapse occurred. This will also result in loss of business as customers’ orders cannot be fulfilled – having a negative impact on the business’ reputation.
If you would like any further information on pallet racking systems and inspections, call 01423 819057 or email sales@warehousestoragesolutions.com to arrange a no obligation visit.